Composite geomembrane is made by combining geotextile and geomembrane through thermal compounding or adhesive bonding processes.
Composite geomembranes have various outstanding advantages. Firstly, it combines the reinforcement effect of geotextiles with the anti-seepage performance of geomembranes, making it more versatile in engineering applications. Geotextiles can enhance the tensile strength of composite geomembranes, preventing them from being stretched and damaged during construction and use, while geomembranes provide reliable anti-seepage barriers.
Secondly, the composite geomembrane has good corrosion resistance and anti-aging performance, and can work stably for a long time under harsh environmental conditions.
Execution standard for composite geomembrane GB/T 17642-2008 |
Mass per unit area(g/m2) | 400
| 500 | 600 | 700 | 800 | 900 | 1000 | 1100 |
Common PE film thickness | 0.2-0.35 | 0.3-0.6 |
|
|
|
|
Common specifications | One cloth, one film | 150/0.25 | 200/0.3 | 300/0.3 | 300/0.4 | 300/0.5 | 400/0.5 | 400/0.6 |
|
Two fabrics and one film | 100/0.2/100 | 100/0.3/100 | 150/0.3/150 | 200/0.3/200 | 200/0.4/200 | 200/0.5/200 | 250/0.5/250 |
|
Nominal fracture strength(KN/m) | 5 | 7.5 | 10 | 12 | 14 | 16 | 18 | 20 |
Longitudinal and transverse fracture strength(KN/m)≥ | 5 | 7.5 | 10 | 12 | 14 | 16 | 18 | 20 |
Longitudinal and transverse standard strength corresponding to elongation% | 30~100 |
CBR top breaking strength rate/KN≥ | 1.1 | 1.5 | 1.9 | 2.2 | 2.5 | 2.8 | 3 | 3.2 |
Longitudinal and transverse tearing strength ratio/KN≥ | 0.15 | 0.25 | 0.32 | 0.4 | 0.48 | 0.56 | 0.32 | 0.7 |
Resistant to hydrostatic pressure/MPa |
| 0.2 | 0.3 | 0.4 | 0.5 | 0.6 | 0.7 | 0.8 | 1 |
One cloth, one film | 0.4 | 0.5 | 0.6 | 0.8 | 1 | 1.2 | 1.4 | 1.6 |
Two fabrics and one film | 0.5 | 0.6 | 0.8 | 1 | 1.2 | 1.4 | 1.6 | 1.8 |
Peel strength /(N/cm) | 6 |
Vertical permeability coefficient/(cm/s) | According to design or contract requirements |
Width deviation/% | -1 |
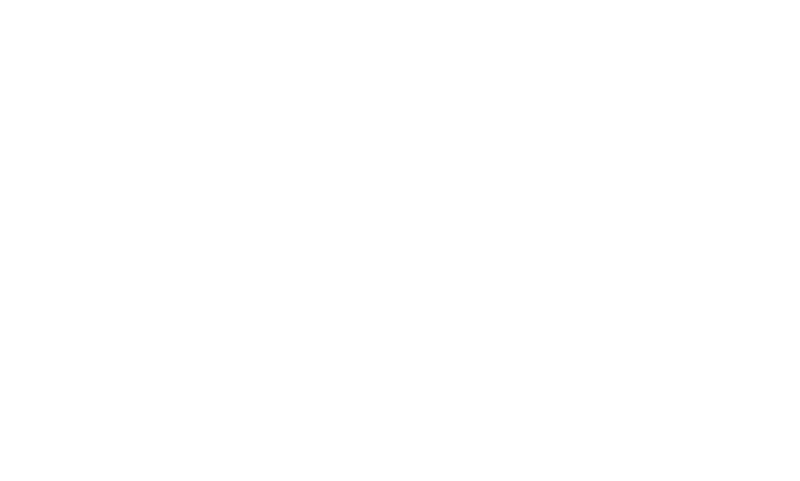
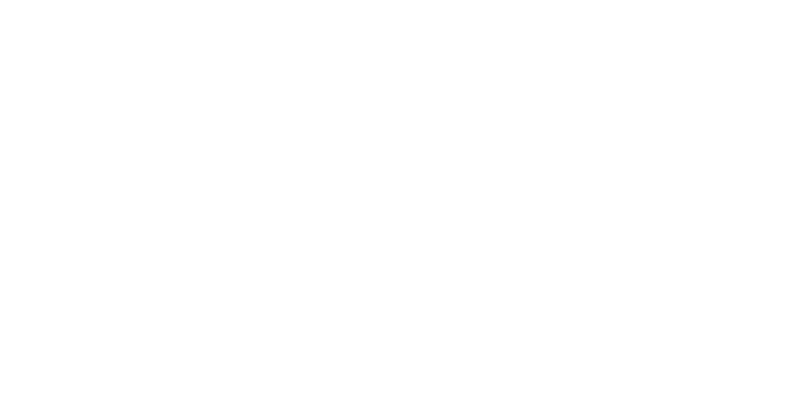
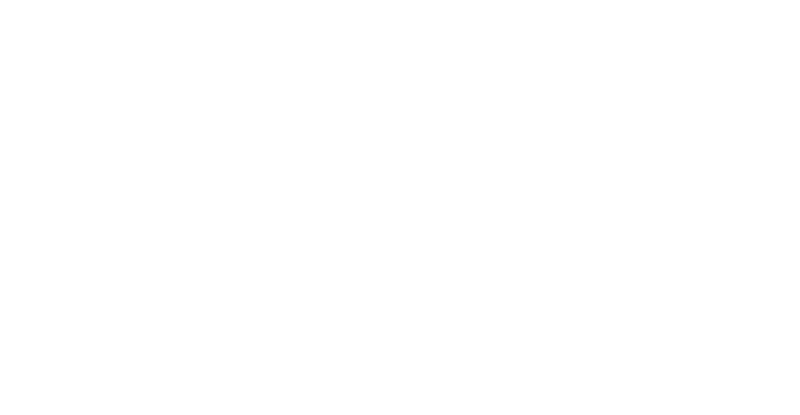
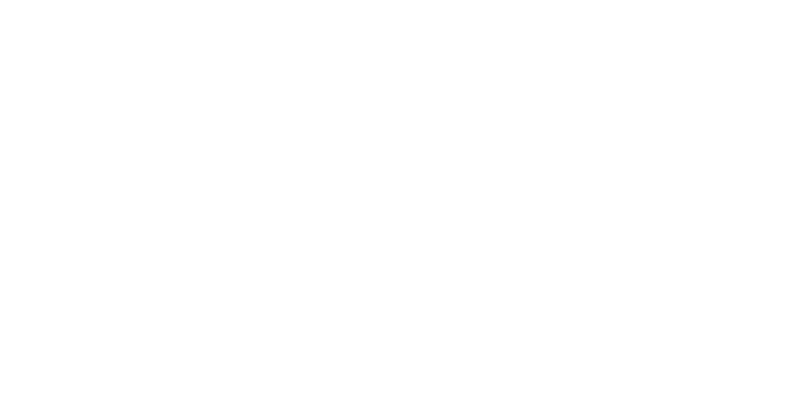
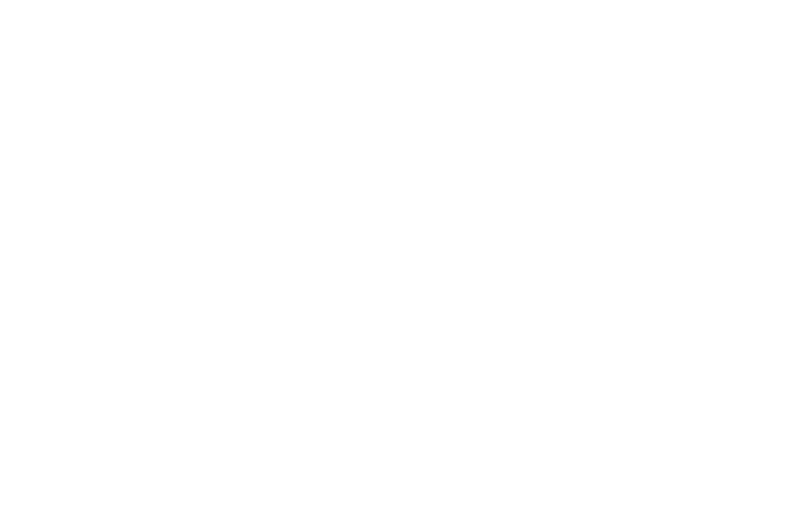

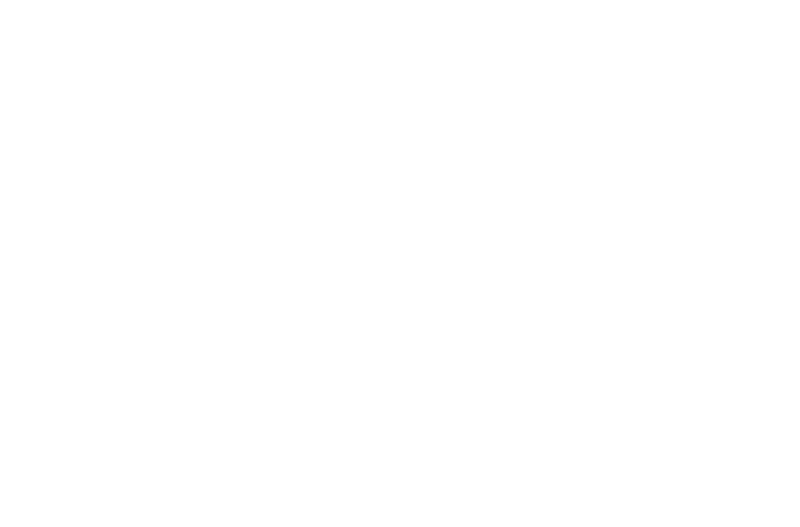
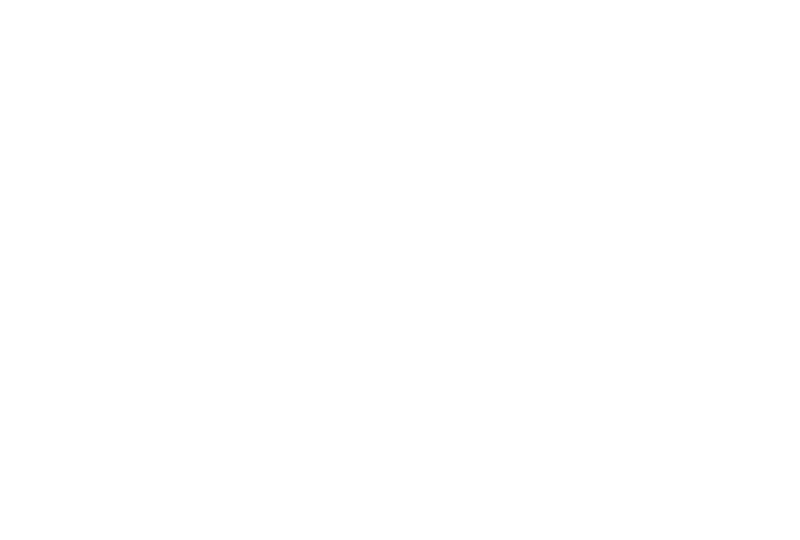
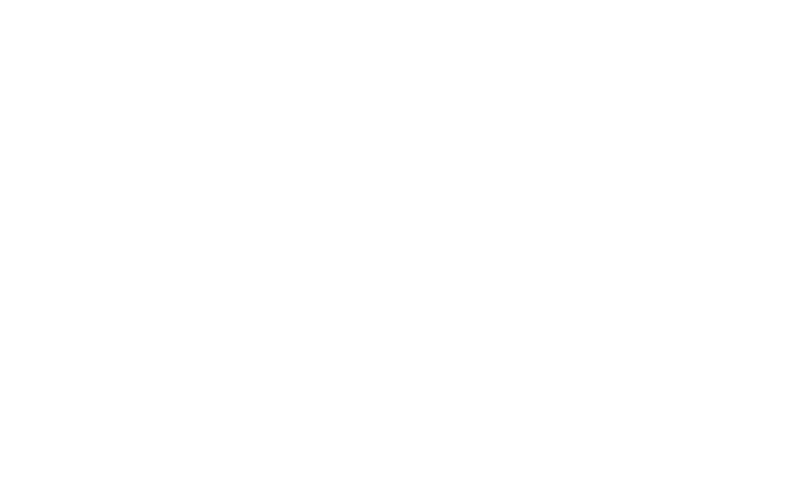
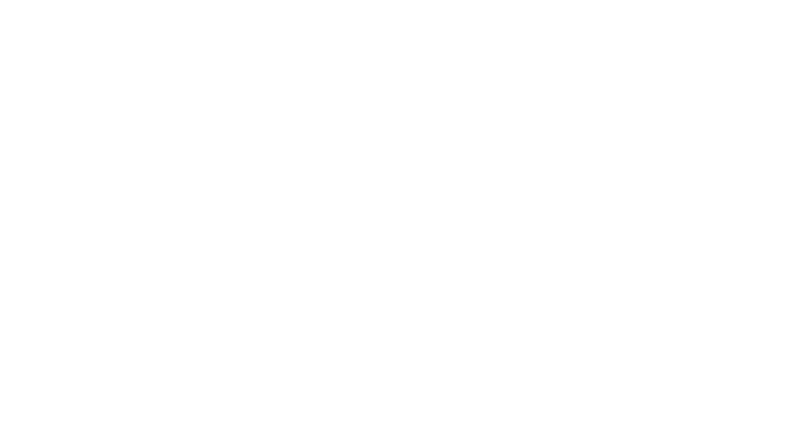